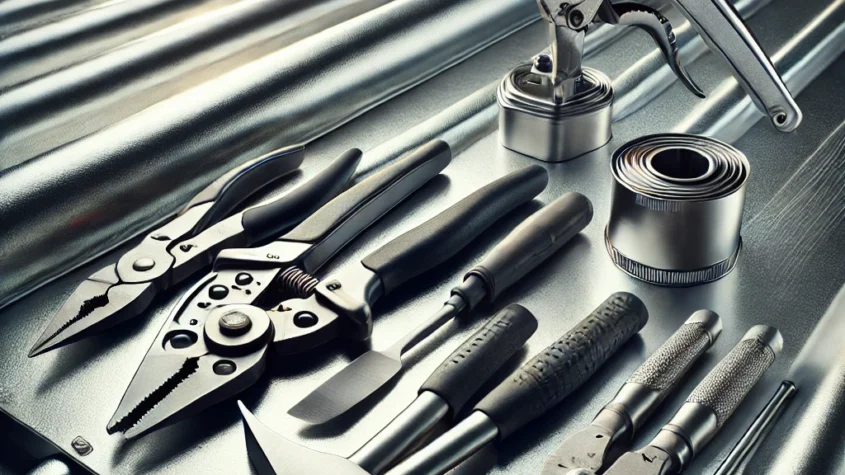
Metal bending equipment plays a crucial role in manufacturing and fabrication processes. From simple bending machines to more complex CNC technologies, these tools allow for precision shaping of metal materials into desired forms. Understanding the types and uses of metal bending equipment can significantly enhance production efficiency and quality.
In industries such as automotive, construction, and aerospace, the demand for accurately bent metal components is high. Metal bending equipment can accommodate various thicknesses and materials, streamlining workflows and reducing wastage. Knowing which equipment suits specific projects is essential for optimizing operations.
The landscape of metal bending technology is continually evolving. Investing in the right equipment not only improves the quality of finished products but also impacts the overall cost-effectiveness of production. By exploring the capabilities of different metal bending machines, businesses can make informed decisions to drive their success.
Types of Metal Bending Equipment
Metal bending equipment is crucial for shaping materials effectively in various industries. Each type has distinct characteristics, usages, and advantages suited to specific tasks.
Manual Benders
Manual benders rely on human power to operate. They are typically used for smaller jobs and are ideal for bending thinner materials like sheet metal and rods.
These devices can be simple lever-based tools or more intricate machines with multiple bending capabilities. Key features include adjustable stops for precision, compact designs for easy storage, and portability for onsite work.
Typical applications involve fabricating parts in smaller workshops or for DIY projects. Their low cost makes them accessible for hobbyists and small businesses alike.
Hydraulic Benders
Hydraulic benders use hydraulic power to bend metals. They are highly efficient and suitable for heavy-duty applications involving thicker materials.
This equipment can achieve considerable force, allowing for more complex bends and shapes. Users appreciate the control and precision offered through hydraulic systems, often equipped with gauges for accuracy.
Common industries that utilize hydraulic benders include automotive repair and construction. Additionally, they are advantageous for producing repeated bends consistently.
CNC Bending Machines
CNC bending machines employ computer numerical control technology for precision bending. They are designed for complex parts requiring high accuracy and repeatability.
These machines can process multiple bend angles and radii, making them suitable for intricate designs. Operators can program them to adjust settings according to the job specifications, increasing efficiency.
Industries such as aerospace and electronics frequently use CNC benders. Their ability to handle various materials, including stainless steel and aluminum, enhances versatility and productivity.
Press Brakes
Press brakes are versatile machines that use a combination of force and a die to bend metals. They can achieve various bends and angles, making them suitable for complex shapes.
These machines come in different sizes, accommodating both small workshops and large-scale production facilities. Key advantages include the ability to bend thicker materials and multi-axis bending capabilities.
Common applications involve producing brackets, frames, and enclosures in manufacturing. Press brakes improve precision and offer a significant productivity boost in metalworking processes.
Roll Benders
Roll benders are designed to create curves by rolling metal sheets through a series of rollers. This equipment is especially effective for bending tubes and large sheets into arcs or circles.
The mechanism typically consists of three rollers, with two acting as the driving rollers and one positioned at the top for pressure. Users can adjust the spacing between the rollers to achieve different diameters.
Industries such as construction and marine engineering utilize roll benders to create structural components. Their ability to produce consistent curves allows for smoother, more efficient fabrication.
Forging and Swaging Machines
Forging and swaging machines are specialized for altering the shape and size of metal by applying compressive forces. Forging is often used for creating stronger parts through deformation, while swaging reshapes metal without removing material.
These machines can create complex shapes and enhance the material’s properties. They are usually employed in high-strength applications such as aerospace components and tool manufacturing.
Common equipment types include hammer forges and rotary swagers. These machines provide significant advantages in durability and efficiency for specific metalworking tasks.
Operational Principles
The operation of metal bending equipment relies on specific mechanical and mathematical principles. Understanding these principles is crucial for effective performance and achieving desired results in metal fabrication.
Mechanical Advantage
Mechanical advantage in metal bending equipment refers to the ratio of output force to input force. It determines how effectively the machine can bend metal with minimal effort.
A common method to achieve mechanical advantage is through leverage. Machines often utilize beams, levers, and pivot points, enhancing the efficiency of the bending process.
For example, a press brake uses a long arm to amplify the bending force applied to the metal sheet.
This allows the operator to exert less physical effort while achieving significant deformation in the material. Properly calculating the mechanical advantage assists in selecting the right equipment for specific tasks.
Bending Force Calculation
Calculating the bending force necessary to deform metal is critical for effective operation. The formula typically used is:
[ F = \frac{K \cdot W \cdot T^2}{D} ]Where:
- ( F ) = Required bending force
- ( K ) = Material constant
- ( W ) = Width of the material
- ( T ) = Thickness of the material
- ( D ) = Die opening
The material constant ( K ) varies depending on the type of metal. This calculation gives operators a precise measure of the force needed for their specific application.
By using appropriate calculations, they can prevent material damage or equipment overloading during the bending process.
Precision and Control
Precision and control in metal bending are achieved through various mechanisms and technologies. CNC (Computer Numerical Control) systems are commonly integrated into bending machines to ensure accuracy.
These systems allow for programmable settings that fine-tune the bending parameters, including angle and length.
Additionally, feedback loops and sensors provide real-time monitoring of the bending process.
Operators can make adjustments as needed, ensuring the finished product meets specifications. Implementing these technologies enhances repeatability and reduces the risk of errors in production.
Couples Counselling Vancouver BC: Effective Strategies for Relationship Improvement
Couples Counselling Vancouver BC, offers a valuable approach to address relationship chall…